Building Management System
A building management system (BMS), also known as a building automation system (BAS), is a computer-based control system installed in buildings that controls and monitors the building's mechanical and electrical equipment such as ventilation, lighting, power systems, fire systems, and security systems. Building management systems are most commonly used in large premises with multitudinous services. Basically IBMS systems operate on pre-set of programs which are designed to receive Input signals from Field devices and other building systems; further the data received is utilized to monitor various equipment including third party systems and Provide control signals for their operations. The Faults or any other Operability conditions are notified through inbuilt alert systems.
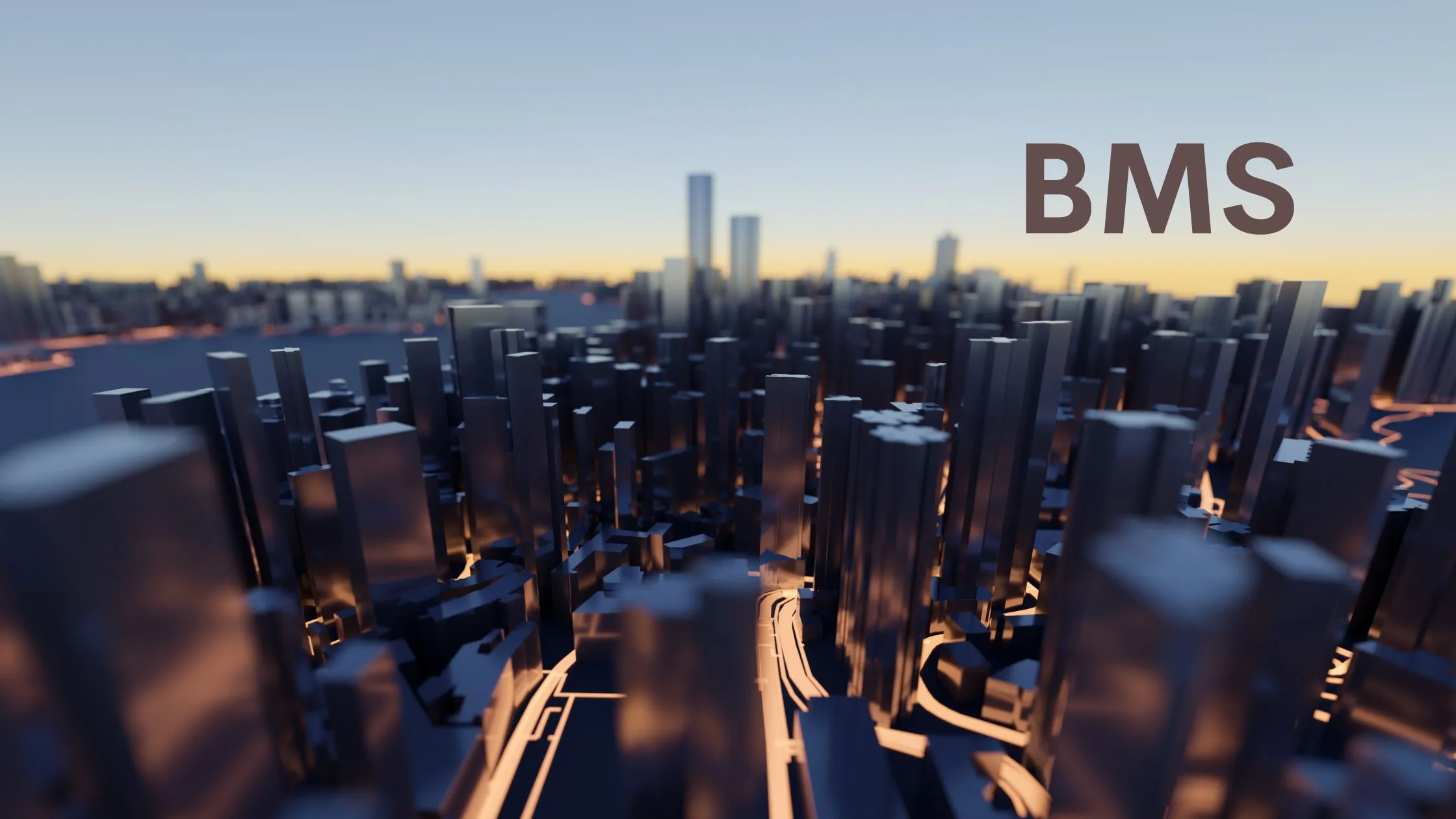
A few main functions of BMS system are
- Boiler controls-maintain a constant temperature and switch boilers on/off at certain times.
- HVAC-Maintain IAQ, control fans and dampers, control air handling units and fan coil units.
- Lighting control-turn lights on/off according to a specified schedule and control Emergency lighting.
- Electric power control-control and monitor core electrical and mechanical equipment.
- Ventilation-adjust based on occupancy controls (DCV).
- Security and observation-access control, surveillance and intrusion detection.
- Fire alarm system-smoke control system, active alarm locations.
- Elevators-elevator video display, status system.
- Plumbing and water monitoring-detect hydraulic flows, open/close valves automatically, monitor/observe temperature deviations.
A few highlights on BMS are
1.Monitoring functionality, Run times and operability conditions of Mechanical equipment.
2.Access and Control the Equipment, Maintain IAQ.
3.Activate fire prevention system such as Fire dampers, Trip required Mechanical equipment during emergency using fire detection system inputs, thus help in reducing fire hazards.
4.Maintain IEQ
5. Improve Energy efficiency by Monitoring and controlling- equipment like DCV systems, VFD’s , Pumps, Chillers etc.